Jiang Xuelin1, Yang Enguo2, Yang Peizhou3
EHDC Jinping Construction Management Authority , Xichang Xinchun P.O.,
Abstract: Jinping-I Hydropower Station dam is concrete arch dam with max. height of 305m, and it is the highest arch dam in the world. Integrity ,deformation modulus, shear strength, and impermeability of foundation rock will all effect the dam safety directly. Large-scale Lamprophyre intrusion in foundation rock will do harm to the dam stability, foundation stress transfer, so it has to be treated to make sure that the dam is safe. It is proved that deformation modulus , compression strength, tensile strength , shear strength and Poisson ratio of lamprophyre could not meet the design requirements after high pressure cement grouting, so chemical grouting had to be adopted to treat the lamprophyre. High permeable epoxy resin is tried to grout the weathered lamprophyre. The physical characteristic of weathered lamprophyre is impenetrable and inhomogeneity, however, the YDS epoxy resin is low initial viscosity, strong affinity to mediums , excellent permeability and good ageing property. After chemical grouting, the rock mechanics characteristics were improved greatly and met the design requirements, it was proved that lamprophyre could be grouted by YDS epoxy resin.
Key Words:highest arch dam lamprophyre high permeability epoxy resin
1.Forward
Lamprophyre and Fault f5 are near the arch abutment of Jinping-I Hydropower arch dam. These soft stratum affect the dam deformation and stability. It was proved by high pressure consolidation grouting that such soft stratum mechanics parameters can not be improved by cement grouting, so excavation and placing concrete were adopted on them partly. But the construction contractor has to face large safety risks during excavation. In addition, excavation and placing concrete operation are slow, and it will cause the construction plan can not be achieved . Considering these problems, high pressure cement grouting combined with chemical grouting is advised to treat large scale and poor strength lamprophyre. More research on its technical feasibility and reliability will be carried out based on site grouting trial.
2. Grouting Trial Purpose
2.1 Grouting Trial Purpose
Studying improvement degree of integrality, rigidity ,impermeability and shear strength of lamprophyre before and after grouting .
Studying the duration and relia- bility of chemical grouted lamprophyre used as arch dam foundation.
Cost comparison between grouting and excavation according to construction efficiency and safety risks.
2.2 Geological Characteristics of Lamprophyre in Trial Zone
Lamprophyre develops in sand slate. Its width is around 2.0~4.0m and it is highly to slightly weathered. In sand slate,itgets more intensively wea- thered. The weathering degree mainly changes from moderate to intense. Rock mass is loose and poor integrality. Small faults around 5~20cm in width develop along the interface between lamprophyre and sand slate, Rock mass in this area is loose, it is classification Ⅳ2. Chemical grouting trial zone is located in gallery at el. 1885.
2.3 Mechanics Characteristics of Lamprophyre before Grouting
Mechanics Characteristics of Lamprophyre are listed on table 2-1
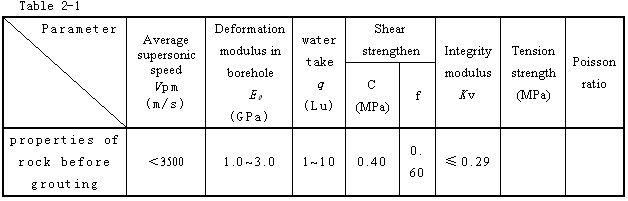
2.4 Physical and Mechanics Characteri- stics of Lamprophyre after Grouting
According to designer requirements, mechanics parameters of Lamprophyre should meet such data listed on table 2-2.
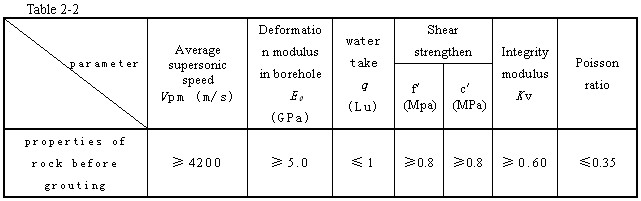
3. Grouting Trial Zone
3.1 Grouting Trial Zone
This grouting trial zone was located at left gallery (1885-2) at el.1885m, which was 120~160m in vertical direction and 110~120m in horizontal direction in mountain before excavation. It is 25~60m in vertical direction and 30~50m in horizontal direction in mountain after excavation . The length of zone is 12m, the thickness of concrete cover is 1.00~1.25m. Its elevation is 1884.3~1884.5m,Grouting holes’ location is shown by drawing 3-1
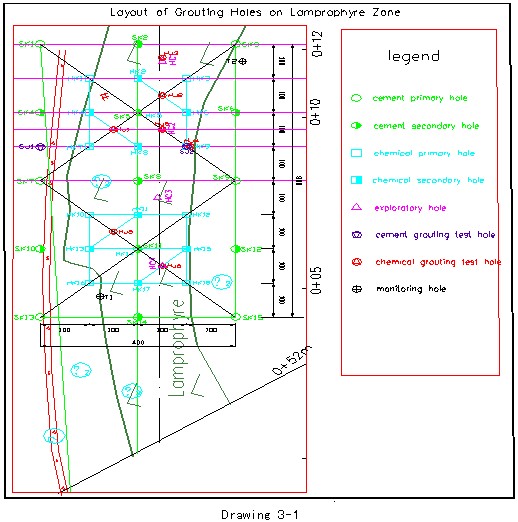
3.2 Simulating Grouting Test in Lab
3.2.1 Lab Experiment of YDS
YDS are prepared from epoxy resin, acetone, furfural, diethylenetriamine and a litter amount of compound rein- forcer YDS (CRY), which plays a very important role in the system. According to lamprophyre characteristics , after lots lab test of different compounding of chemical material , three prescribes of better performance(YDS-7 , YDS-7-1,YDS-7-2) are used to simulating grouting in lab.
3.2.2 Simulating Chemical Grouting Trial
Typical weathered lamprophyre had been marinated for 7 days in common temperature under no grouting pressure. After 90 days curing in air, its mainly mechanics parameters are shown on table 3-2,these parameters can meet design requirements.
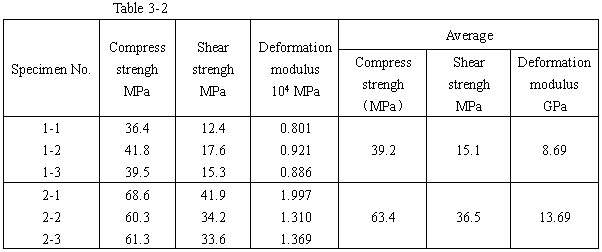
3.3 Field Grouting Trial Design
Considering the lamprophyre should be softened once it meet water and in order to prevent YDS runs away from the lamprophyre area, no chemical grouting can be started if the grouting section’s Lugeon is larger than 1 Lu. So high pressure cement grouting have to be undertaken before chemical grouting.
PO42.5 Portland cement is used for high pressure cement grouting, its fineness requirement is that remained quantity should not be larger than 5% after it pass through square sieve pore of 80μm.
High permeable epoxy resin grouting materials YDS is used for lamprophyre , it is a patent of one of Chinese famous institute and has good properties including their low initial viscosity, strong affinity to mediums ,excellent permeability and good ageing property.
4. Construction Method ,Workmanship and Main Technical Requirements
4.1 Cement Grouting
The lamprophyre cement grouting method is stage grouting.
The max. grouting pressure is 5~6Mpa.
Water/cement ratio is 2:1、1:1、0.7:1、0.5:1.
Grouting hole is inclined and their direction is along lamprophyre ,the max hole depth in vertical direction is 35 m.
The section length from the top to bottom is 2m, 3m, 3m, 5m.
Hole diameter is φ76mm.
Spacing between primary holes is 4m, spacing between secondary holes is 2m.
There are 9 cement grouting holes in this zone, total length is 326m.
The average cement take is 617Kg/m in primary holes, 176Kg/m in secondary holes.
4.2 Chemical Grouting
The workmanship of lamprophyre chemical grouting is listed as follow:
Drilling hole →flush hole-simply water pressure test→compounding chemical material→ drainage water in hole → grouting → replace chemical grouting in hole → break for 8h→next stage ……→seal hole.
The lamprophyre chemical grouting method is stage grouting.
The maxi. grouting pressure is 3~3.5Mpa.
The section length from the top to bottom is 2m, 3m, 3m,5m ,the max hole depth in vertical direction is 30 m.
Grouting hole is inclined and their layout is along lamprophyre.
Hole diameter is φ56mm.
YDS-7 is used for common sections, YDS-0 is used for those sections with large grout take as the viscosity of YDS-0 is much higher than YDS-7.
Spacing between primary holes is 2m, spacing between secondary holes is 1m.
There are 9 chemical grouting holes in this zone, total length is 280m.
The average YDS take is 123Kg/m in primary holes, 40Kg/m in secondary holes.
Section grouting completion criterion is that keeping grouting for 30min grouting when refusal or grout take is less than 0.01~0.05L/ min.m.
Section length and grouting pressure is list on table 4-1.
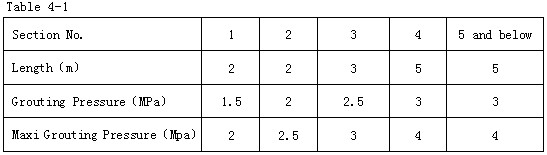
5. Grouting Effect Examination
The examination methods of grouting results are water pressure before and after grouting, supersonic test, deformation modulus test in holes, lab test for bore cores.
Chemical grouting results should be evaluated base on those test data.
5.1 Water pressure
During grouting construction, water pressure is carried out in pilot holes, cement grouting holes and chemical grouting holes before and after grouting. Lugeon data in different stage are shown on statistic table 5-1. After cement and chemical grouting , lamprophyre is impervious and its Lugeon is lower than 1 Lu.
5.2 Physical Detection Result
During and after chemical grouting, supersonic and deformation modulus and television detection are carried out in all holes. Statistic data is shown on table 5-2.
Cement concretion is filled in open fissures by cement grouting, after chemical grouting, gel is filled in small fissures and micro pore, so the mechanics parameters of lamprophyre improve greatly.
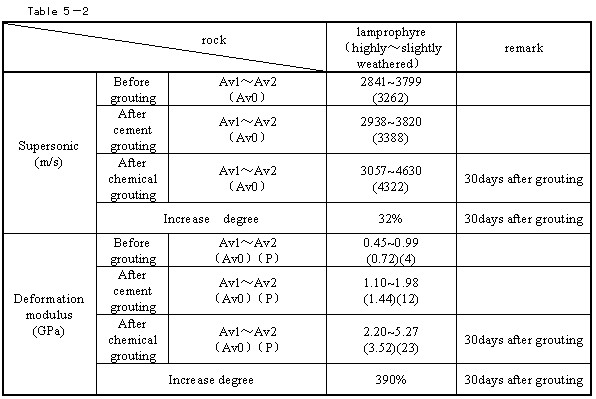
5.3 Bore Core Lab Test
120 days after chemical grouting, 24 specimens prepared of bore cores are used to carry out lab test, the results are that 70% of specimen’s deformation modulus is larger than 6Gpa and 30% is between 5 to 6Gpa. The deformation modulus meets this arch dam design requirements.
6. Conclusion
It is shown by television and bore core that cement concretion is filling in open fissures and gel is filling into small fissures and micro pore satisfactorily. Fissures are bonded tight. So its supersonic and integra- lity and deformation modulus are improved greatly. The proportion and ingredients of chemical material YDS is successful, the grouting workmanship and construction parameters are suitable.
Impermeability of lamprophyre can be improved by cement grouting partly however the improvement of supersonic and deformation modulus of lamprophyre is limited , because small fissures and micro pore developed in weathered rock.
As YDS has good properties including low initial viscosity and high permeable, supersonic and deformation modulus of lamprophyre are improved greatly after chemical, all test parameters meets the design requirements.
Although chemical grouting has a shortcoming of long construction period and expensive cost, it can reduce safety risks during excavation of tunnels and high slope under poor geological condition and avoid construction interfere and prompt the construction progress of the whole project. So the chemical trial achievement has rather higher application value.
7. Advise for Grouting Trial
7.1 Microfine Cement Should Be Used For High Pressure Grouting
Generally, common Portland cement can be grouted into fissures with width larger than 200μm. As to fissures with width is about 100μm, the results of common cement grouting is not good, however chemical material can be grouted into micro fissures with width less than 1μm. The chemical grouting area is not sealed tight by cement grout, so chemical material is extruded away from lamprophyre area, which affect grouting result adversely. In addition , the average unit YDS take is 77L/m and outclass its theory quantity .
So , it is suggested that microfine cement should be used for high pressure grouting before chemical grouting to make sure that the chemical grouting area is sealed tight.
7.2 Improve the Chemical Material Compounding
In this grouting trial and research, three compounding of YDS series (YDS-7,YDS-7-1,YDS-7-2)are applied, their characteristics are low initial viscosity, strong affinity to medium, excellent permeability. Those good characteristics settle the major issue of this trial that small fissures and micros pore can not be grouted by cement.
However the mechanics parameters of its solid increase slowly and can not reach the design mechanics parameters for a long time, so compounding should be improved to expedite the increasing speed.